The sounds of the shuttle looms roaring like muscle cars, blue dusts from indigo dancing in the whole room, this is one of the best mills in Japan, Shinya mills. It’s also where our 50’s and 20’s & 30’s fabric are woven.
There are a few things about Shinya I was quite surprised about.
First, the number of machines they have and its machine brand. They have about 70 of these “Ensyu” vintage shuttle looms. I have visited several mills before but 70 is by far the biggest number for sure. You may have heard of the name, GL-3 Toyoda but probably not ‘Ensyu’. By the way, Ensyu means the area close to Mt.Fuji. The mountain represents to Japanese people something mighty or second to none so I think this brand name proudly contains the kind of meaning to it.
Anyways, it’s a denim specific weaving machine and these machines at Shinya mills are custom made only for them, allowing mechanics to have much more control to the tense and the density of weaving, which contributes so much to giving a sense of inconsistency and roughness to the fabric like vintage denim fabrics. On the flop side of working with these special machines, the craftsmen have to be skilled and sensitive to the conditions of the machines, the change of the climate, and of the humidity of the day, otherwise the machines would end up producing a totally different product even if the same threads were used.
Actually, Shinya mills have more than 100 of these special machines. but you might wanna say, "Hey man, you said 70 machines were working just now and what's the truth then?" Well, 70 are operable and the rest are there only for taking the replacement parts from. These machines are the heritage from over a century ago. Therefore, in order to maintain these special machines, they need to have however broken shuttle looms to make the machines running longer. They say as for now they have enough parts to sustain their business for another 10 years to come. but after that...?
This is one of the reasons why it's said that JP denim mills will disappear in 10 years.
The craftsmen there were all wearing some rubbery workwear. I think that's because so much blue dusts are floating everywhere in the room that you'll have indigo booger for sure at the end of a day. So, a facial mask is also a must despite the Covid situation.
It's a bit sensitive topic to write about because I'm Japanese and I think we are a bit lagged behind with the gender equality compared to some other countries but it was the first time for me to see female craftsmen working in the denim weaving industry. As the denim world of today is still mostly dominated by men, so is the manufacture side in general but Shinya mills is a bit different in this sense as well.
The picture above shows the former president of Shinya mills, Etuko-san and on the right, her daughter, Aiko-san, who's taken over the presidency since the end of June, 2020. Unlike other JP mills, Shinya mills have been run by these two ladies since 2012 when the legendary craftsman/ the founder of Shinya mills, Yoshiaki-san, passed away. Even when Yoshiaki-san was alive and well, Etsuko-san was working as a sales manager, which was also quite unusual to see in the denim industry back then.
I asked her a few questions I've been curious about.
Ryo(R): Why do you think Japanese denim brands would rather hide where its denim fabric is woven? Overseas brands mostly mention where the fabric is made, or by what machine it is woven, in order to show the appreciation to the maker, and to be transparent with their customers, etc. This also leads to giving more incentive to customers for buying the product as well but most of JP brands zip their mouths up when it comes to talking about denim mills.
Etsuko-san(E): In the past, it was more restricted by brands. I mean denim brands would rather hide any information of fabric makers because knowing a good mill was the very asset for denim brands. Back then, any information about good denim mills was a key factor for success. If you told about it, other guys would come and try to make the similar fabrics.
Etsuko-san also told me an interesting story about how Shinya mills have achieved the title of the best denim mill in the world.
E: Actually, in 1992, our factory was burned once and lots of machines got broken from the fire. One of the denim weaving machines caught fire and it rapidly spread all over our mill. We had to stop our business for a while and we even thought at one point to close this business. After a while, even though the scale of the business shrank, we started to run the business again but with more innovated looms. After the fire, we tried to focus on weaving different kinds of fabric like duck, canvas, etc.
R: Oh.. that was such a tragedy. but what was the trigger for Shinya mills to focus again on denim fabric?
E: Well, before the fire we had been working with whom people of today call denim legends. People from those denim brands pushed theirselves so hard to find some replacement fabric but it seemed it was impossible to find any other fabric as good as ours. I've once had a dinner with one of the legends but tears was running down on his cheek saying his business was finally getting on the right trajectory thanks to the top notch quality fabric of Shinya, but my dream might end up here. In 1990, vintage reproduction, vintage American clothings were taking Japanese people by hip storm, which would spread all over the world.
Also, one day some brands asked me if we had any leftover fabrics before the fire. We had some but they were all half burnet and were of no value as a product. So, I thought I'd give them out for free but the people from the brands kindly bought all the half useless fabrics because it seemed our fabrics were really something special to them. Having been asked and supported by so many good people around us, we finally started to produce denim fabric in 1992, 2 years after the fire.
The denim legend once talked about us on a magazine, saying that the world best mill was once burnt and the guy was the pioneer in the vintage repro industry so other denim brands were dying to find who the maker was only from the information that the mill was once burnt. But since then, we have gradually gained the fame in making vintage-alike denim in the industry.
Etsuko-san & Yoshiaki-san
E: Ever since we resumed making denim fabric, so many guys were looking after the secret to produce vintage-alike denim from us. Some tried to break into our facility with some tools to imitate the machine setting. Their effort was basically useless because our machines are Ensyu and it has a different construction from other shuttle looms but still people were dying to reach its secret. At the end, we put a poster at the door saying "No one can enter this facility without the permission of Etsuko. ( It seems she was once famous for being really tense all the time, haha)
Sometimes we had some mechanics invited to our mills to check the machines but everyone says "Wow you must have poured so much money and effort into these machines! They have very little trace of its original form!"
In the past 4 factory visit, a denim novice like me didn’t see much difference among them partly because I guess they all used the same machine, GL-3 but I could easily capture one difference on the fabric woven here: the selvedge parts are so stiff that the edges curl up or down a bit and it’s really finely and tensely woven. I’m sure it does make a significant difference on jean fade like rail truck fades on the outseam.
Almost all 70 machines were at its duty on the day we visited but this mill appeared so sacred to me because I noticed that the fabrics from almost all the best JP denim brands, like every renowned JP’s denim brand’s are woven here.
TCB was I think the youngest brand of all among other brands. Denim world is easy to tell in this sense because selvedge talks the brands!
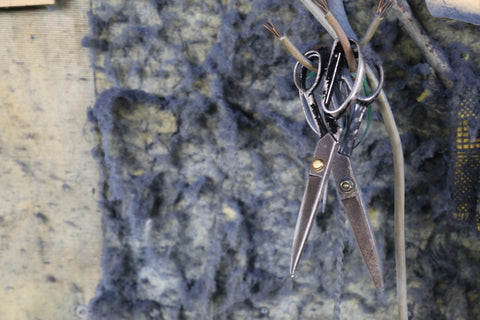
Leave a comment